Table Of Contents:
- Key Takeaways
- Introduction to Man Lift Rental Regulations
- Federal Safety Standards Affecting Man Lift Rentals
- Navigating State-Specific Man Lift Rental Laws
- How to Research Your State’s Man Lift Laws
- Consequences of Non-Compliance With State Laws
- Best Practices for Complying With Man Lift Rental Laws
Are you aware that man lift rental laws can vary significantly from state to state? Understanding these regulations is crucial for businesses in the construction and maintenance industries. This article will explore federal safety standards, state-specific rental laws, and best practices for compliance. By the end, you’ll know how to research your state’s regulations and avoid potential legal issues. Stay informed to ensure safe operations and avoid costly penalties when leasing man lifts for your projects.
Key Takeaways
- Understanding state-specific man lift rental laws is crucial for construction professionals to ensure compliance and safety
- Regular inspections and maintenance of man lifts are essential to meet state regulations and prevent accidents
- Proper operator training and certification are vital for complying with state laws and maintaining a safe work environment
- Selecting reputable rental providers helps ensure equipment meets local requirements and safety standards
- Implementing comprehensive safety protocols on job sites is necessary to comply with state-specific man lift rental laws
Introduction to Man Lift Rental Regulations
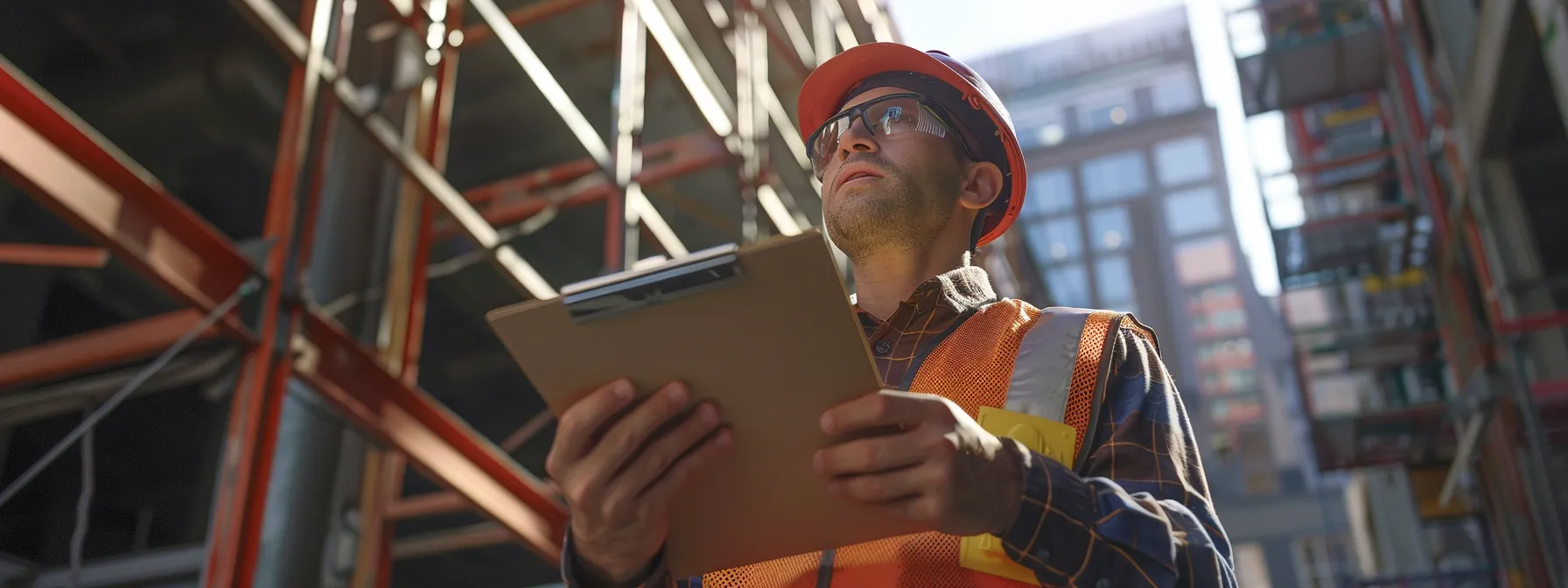
Understanding man lifts and their common uses is crucial for construction professionals. State-specific laws govern the rental and operation of these machines, impacting employment practices and reasonable accommodations View on Google Maps. Proper documentation and interviews are often required to ensure compliance with local regulations. Familiarity with these laws is essential for safe and legal man lift operation.
Understanding Man Lifts and Their Common Uses
Man lifts are essential equipment in construction and maintenance industries, providing safe vertical access for workers. These Innovative Reach machines are commonly used for tasks such as painting, electrical work, and window installation, offering a secure alternative to ladders or scaffolding. In states like South Carolina, specific regulations govern man lift rentals, ensuring safety and compliance.
When renting a man lift, construction professionals must consider various factors, including the project’s height requirements and the machine’s weight capacity. Landlords and property managers often utilize man lifts for building maintenance, such as cleaning exterior windows or repairing roofs. It’s crucial to understand local laws regarding man lift operation, especially in cases involving tenant evictions or property inspections.
Man lifts come in various types, including boom lifts, scissor lifts, and vertical mast lifts, each designed for specific applications. Operators must undergo proper training and certification to use these machines safely and efficiently. In some instances, such as post-conviction rehabilitation programs, man lift operation skills can provide valuable employment opportunities for individuals seeking to reenter the workforce.
Recognizing the Importance of State-Specific Laws
State-specific laws play a crucial role in regulating man lift rentals, ensuring safety and compliance across various industries. These laws often address issues such as security deposits, animal restrictions, and revenue reporting requirements for rental companies. Construction professionals and property managers must familiarize themselves with local regulations to avoid potential legal issues.
The Code of Federal Regulations provides a foundation for man lift safety standards, but individual states may have additional requirements. For example, some states may have specific regulations for man lift use in nursing homes or healthcare facilities. Understanding these nuances is essential for operators and rental companies to maintain compliance and prevent accidents.
State laws also impact the rental process, including documentation and training requirements. Rental companies must adhere to state-specific guidelines when collecting security deposits, handling revenue, and addressing animal-related concerns on job sites. The following table illustrates key areas affected by state-specific man lift rental laws:
Area of Regulation | Examples of State-Specific Requirements |
---|---|
Safety Standards | Operator certification, equipment inspections |
Rental Agreements | Security deposit limits, liability clauses |
Operational Restrictions | Height limits, weight capacities |
Industry-Specific Rules | Healthcare facility regulations, construction site requirements |
Federal Safety Standards Affecting Man Lift Rentals
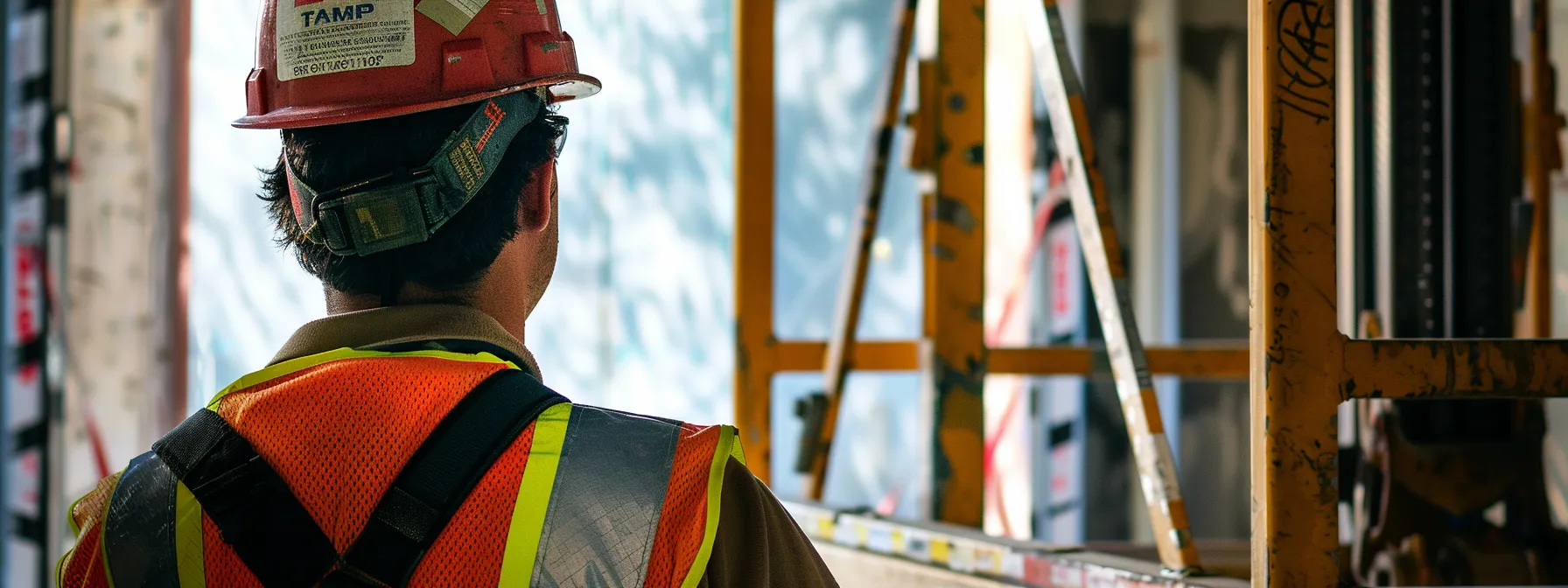
Federal safety standards significantly impact man lift rentals across states, including West Virginia. These regulations, set by OSHA and ANSI, govern equipment operation and safety protocols. Understanding these standards is crucial for construction professionals, telecommunications workers, and property managers to ensure compliance and safe operation in various dwellings and work environments.
Overview of OSHA Regulations for Man Lifts
OSHA regulations for man lifts establish crucial safety standards that impact rental practices across various states. These regulations address key aspects of man lift operation, including accessibility requirements for workers with disabilities and proper management of equipment. Rental companies must ensure their man lifts comply with OSHA standards to maintain a safe work environment.
The OSHA statute outlines specific requirements for man lift design and operation, covering elements such as platform guardrails, controls, and emergency descent systems. These regulations also address the need for proper toilet facilities on job sites where man lifts are used, emphasizing the importance of worker comfort and hygiene. Compliance with these standards is essential for rental companies to avoid penalties and ensure worker safety.
OSHA regulations extend to the training and certification of man lift operators, emphasizing the importance of proper education in safe equipment use. This includes guidelines for operating man lifts in various environments, from construction sites to maintenance work in multi-story buildings. The regulations also cover the use of man lifts for accessing elevated beds in healthcare facilities, highlighting the diverse applications of this equipment:
- Operator training and certification requirements
- Equipment inspection and maintenance protocols
- Fall protection measures for workers on elevated platforms
- Guidelines for safe operation in different work environments
- Accessibility considerations for operators with disabilities
Applying ANSI Standards in Equipment Operation
ANSI standards play a crucial role in equipment operation for man lifts, complementing OSHA regulations and enhancing safety in construction and maintenance industries. These standards address various aspects of lift operation, including ADA compliance for accessibility and certification requirements for operators. Rental companies must ensure their equipment and operational procedures align with ANSI guidelines to maintain safety and legal compliance.
The application of ANSI standards in man lift operation extends to specific construction scenarios, such as working near power lines or on uneven terrain. These guidelines often require additional safety measures and operator training, which may incur additional fees for rental companies and end-users. By adhering to ANSI standards, businesses can minimize risks and improve overall efficiency in lift operations.
ANSI standards also influence the design and manufacturing of man lifts, ensuring that equipment meets rigorous safety criteria. This includes specifications for load capacity, stability, and emergency controls. Construction professionals and rental companies must stay informed about updates to ANSI standards to ensure their equipment and practices remain compliant, protecting workers and avoiding potential legal issues.
Navigating State-Specific Man Lift Rental Laws
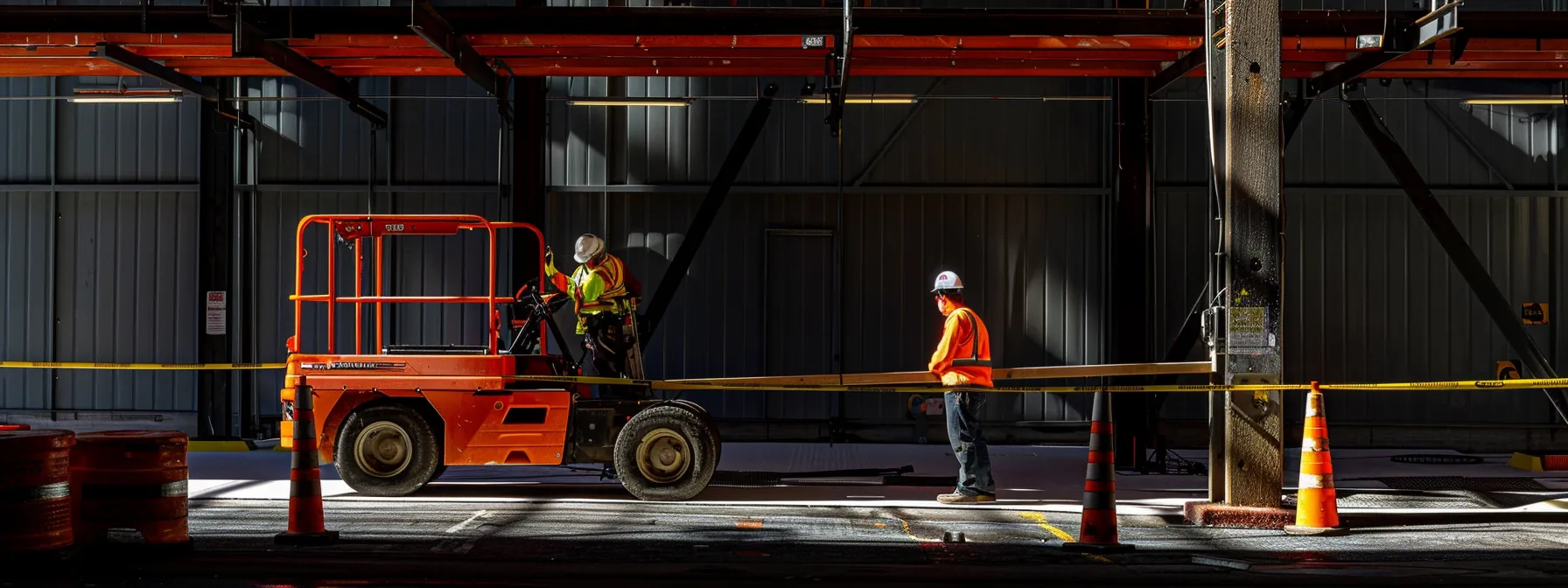
Navigating state-specific man lift rental laws requires understanding licensing requirements, safety training mandates, and inspection obligations. These regulations aim to prevent negligence and ensure safe equipment design. Compliance involves proper documentation, regular maintenance, and adherence to payment terms. Failure to meet these standards may result in damages or legal appeals. Construction professionals must familiarize themselves with local laws to operate safely and efficiently.
Identifying Licensing Requirements by State
Identifying licensing requirements for man lift rentals varies significantly by state, with each jurisdiction enforcing unique regulations. Construction professionals must research and comply with local laws, which often include obtaining specific licenses and maintaining proper liability insurance. These requirements aim to ensure safety and equal opportunity in the workplace while holding operators accountable for their actions.
The licensing process typically involves demonstrating competency through written exams and practical tests, with some states requiring a minimum operator-to-equipment ratio. Safety training is a crucial component of licensing, covering topics such as equipment inspection, emergency procedures, and fall protection. Rental companies must verify that operators possess valid licenses before allowing them to use man lifts on job sites.
State regulations may also mandate periodic license renewals and continuing education to keep operators informed about the latest safety standards and technological advancements. Construction professionals should maintain detailed records of their licensing status and training history to ensure compliance with state-specific requirements and avoid potential legal issues or project delays.
Complying With State-Mandated Safety Training
State-mandated safety training for man lift operators varies across jurisdictions, impacting equipment rental prices and operational procedures. Construction professionals must complete comprehensive training programs that cover equipment operation, maintenance, and emergency protocols. These programs often include language interpretation services to ensure all operators, regardless of their primary language, fully understand safety requirements.
Safety training requirements typically encompass both classroom instruction and hands-on practice with various man lift types, including those used in retail environments and for elevator maintenance. Operators learn to assess job site conditions, perform pre-operation inspections, and navigate potential hazards. Some states mandate refresher courses at regular intervals to keep operators updated on the latest safety standards and equipment innovations.
Compliance with state-mandated safety training often requires documentation of completed courses and certifications. Construction companies and rental agencies must maintain accurate records of operator training to avoid penalties and ensure workplace safety. Many states have implemented online training modules and virtual reality simulations to enhance the effectiveness of safety programs while maintaining social distancing guidelines.
Meeting Inspection and Maintenance Obligations
Meeting inspection and maintenance obligations is crucial for man lift rental companies and operators. Regular inspections ensure the equipment‘s safety and functionality, including checking for paint condition and structural integrity. Companies must establish a robust maintenance policy that addresses routine checks, emergency repairs, and color-coding systems for easy identification of inspection status.
State regulations often require detailed documentation of inspection and maintenance activities. Operators must conduct pre-use inspections, while rental companies are responsible for more comprehensive periodic checks. These inspections may include examining truck-mounted lifts for proper attachment and stability, ensuring all emergency systems are functioning correctly, and verifying that all safety features are operational.
Compliance with state-specific maintenance obligations often involves adhering to manufacturer guidelines and industry standards. Rental companies must maintain a fleet of well-maintained lifts, addressing issues promptly to prevent accidents and downtime. The following table outlines key components of a comprehensive inspection and maintenance program:
Component | Inspection Frequency | Maintenance Action |
---|---|---|
Structural Integrity | Daily | Visual check, repair as needed |
Hydraulic Systems | Weekly | Fluid levels, leak checks |
Emergency Controls | Monthly | Functionality test, recalibration |
Paint and Corrosion | Quarterly | Touch-ups, rust prevention |
How to Research Your State’s Man Lift Laws

Researching state-specific man lift laws is crucial for compliance and safety. This section explores utilizing state government resources, contacting local regulatory agencies, and keeping up with legislative changes. Understanding these processes helps construction professionals navigate regulations, including passenger safety standards and occupancy limits set by the American National Standards Institute, particularly in states like North Carolina. Effective research can prevent lawsuits and ensure adherence to current standards.
Utilizing State Government Resources for Accurate Information
State government websites serve as invaluable resources for construction professionals seeking accurate information on man lift rental laws. These official portals provide detailed specifications for equipment operation, safety protocols, and licensing requirements. By utilizing these resources, businesses can make informed investment decisions and avoid costly compliance issues.
Many state labor departments offer comprehensive guides on man lift regulations, including expense breakdowns for licensing and certification. These resources often include searchable databases of approved training providers and equipment manufacturers, streamlining the process of finding compliant machinery and qualified operators. Accessing this information can significantly reduce the time and cost associated with regulatory research.
Some states have dedicated construction safety divisions that maintain up-to-date information on man lift laws and industry standards. These divisions often provide free consultations to help businesses navigate complex regulations and lobby for necessary changes. By leveraging these services, construction professionals can ensure their operations align with current legal requirements while minimizing compliance-related expenses.
Contacting Local Regulatory Agencies for Guidance
Contacting local regulatory agencies provides construction professionals with direct access to expert guidance on man lift rental laws. These agencies offer invaluable insights into state-specific regulations, including requirements for property management companies and accommodations for operators with physical disabilities. By reaching out to these authorities, businesses can ensure compliance with local standards and avoid potential legal issues.
Regulatory agencies in states like New Jersey and South Dakota often maintain dedicated hotlines and email support for inquiries related to man lift operations. These services can provide clarification on topics such as air conditioning requirements for enclosed lifts and specific weight limits for different equipment types. Utilizing these resources helps construction professionals make informed decisions about equipment selection and usage.
Many local agencies offer on-site consultations to assess compliance with man lift regulations. These visits can be particularly beneficial for businesses operating in multiple states, as they provide personalized guidance on navigating varying legal landscapes. By proactively engaging with regulatory agencies, construction companies can demonstrate their commitment to safety and potentially mitigate fines or penalties associated with non-compliance.
Keeping Up With Changes in Legislation
Construction professionals must stay informed about legislative changes affecting man lift rental laws to ensure compliance and safety. In Ohio, for example, recent updates have addressed the use of lifts on stairs and near credit card processing areas. Monitoring state government websites and industry newsletters helps businesses stay current with evolving regulations.
Changes in legislation often impact operational aspects such as engine requirements and volume restrictions for man lifts. Construction companies should establish a system to track and implement these updates promptly. This may involve designating a team member to review legislative changes regularly and disseminate information to relevant staff.
Professional associations and legal firms specializing in construction law offer valuable resources for keeping up with legislative changes. These organizations often provide summaries of new laws and their potential impact on man lift rentals. Subscribing to their updates can help construction professionals anticipate and prepare for upcoming changes in regulations:
Resource Type | Update Frequency | Information Provided |
---|---|---|
State Government Websites | As laws change | Full text of new regulations |
Industry Newsletters | Monthly | Summaries of legislative updates |
Legal Firms | Quarterly | Analysis of regulatory impact |
Professional Associations | Bi-annually | Compliance guidance and best practices |
Consequences of Non-Compliance With State Laws
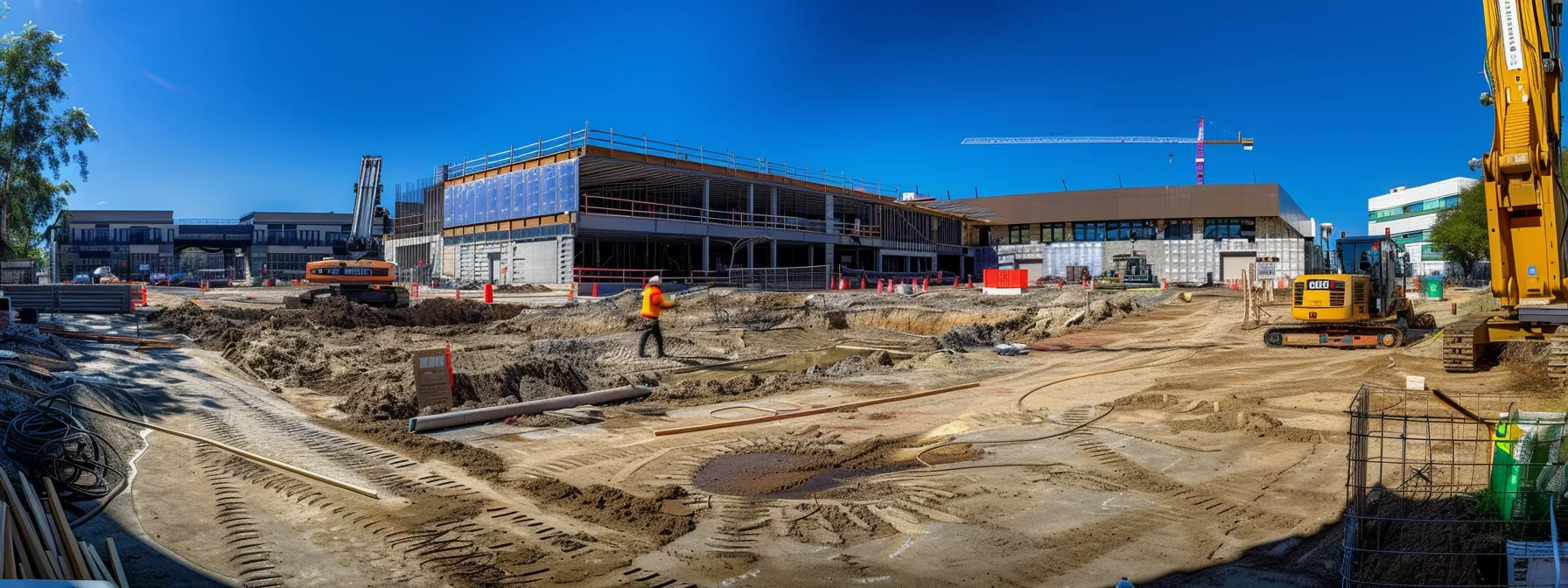
Non-compliance with state-specific man lift rental laws can result in severe consequences for construction businesses. From facing legal penalties and fines to damaging business reputation and operations, the impact can be significant. In states like Virginia and Oregon, violations may affect property management and building projects, potentially disrupting work involving emotional support animals. Understanding these repercussions is crucial for maintaining legal and efficient operations.
Facing Legal Penalties and Fines
Non-compliance with state-specific man lift rental laws exposes employers to significant legal penalties and fines. These consequences can include hefty monetary penalties, which may increase with repeated violations, potentially reaching the ceiling set by state regulations. Construction companies operating in public spaces face heightened scrutiny, as their non-compliance can directly impact public safety and rights.
The severity of fines often correlates with the level of risk associated with the violation. For instance, failure to provide proper fall protection or operating equipment without valid certifications can result in substantial penalties. State labor departments typically enforce these regulations, conducting surprise inspections and issuing citations for violations that endanger workers or the public.
In addition to monetary fines, non-compliant companies may face operational restrictions or license suspensions. These penalties can significantly disrupt business operations, leading to project delays and loss of contracts. Employers must prioritize compliance to avoid these severe consequences, which can have long-lasting impacts on their ability to operate in the construction industry.
Impact on Business Reputation and Operations
Non-compliance with state-specific man lift rental laws can severely damage a company’s reputation, leading to a loss of trust among clients and partners. Construction managers may face increased pressure from administrative bodies to rectify violations promptly, potentially diverting resources from ongoing projects. This damage to reputation can result in fewer contract opportunities and reduced competitiveness in the industry.
Operational disruptions often follow reputation damage, as companies may need to halt work to address compliance issues. Court proceedings related to violations can consume significant time and resources, impacting project timelines and profitability. Additionally, non-compliant businesses may face challenges in securing permits for future projects, especially in areas with strict gravel extraction or environmental regulations.
The long-term effects of non-compliance can extend to employee retention and recruitment. Skilled workers may be hesitant to join or remain with companies known for safety violations or legal issues. This can create a cycle of operational challenges, as businesses struggle to maintain a qualified workforce while addressing compliance concerns, further impacting their ability to compete effectively in the construction market.
Best Practices for Complying With Man Lift Rental Laws

Complying with man lift rental laws requires a multifaceted approach. This section explores selecting reputable providers, ensuring proper operator training, and implementing safety protocols. These practices help construction professionals navigate regulations, including accessibility requirements and credit considerations, while maintaining a harassment-free work environment. By following these guidelines, companies can directly address compliance challenges, including accommodations for workers with deafness.
Selecting Reputable Rental Providers
Selecting reputable rental providers is crucial for construction companies to ensure compliance with state-specific man lift rental laws. These providers should have a proven track record of maintaining their equipment to the highest standards, including regular inspections and prompt repairs. Reputable companies often provide detailed maintenance logs and equipment drawings, which can be invaluable for addressing any anxiety about safety or regulatory compliance.
Construction professionals should prioritize rental providers who demonstrate a thorough understanding of state-specific regulations and prohibitions. This knowledge is essential for ensuring that the rented equipment meets all local requirements, particularly in areas with strict landlord responsibilities or tenant protection laws. Reputable providers often offer guidance on navigating these regulations, helping clients avoid potential legal issues.
When selecting a rental provider, construction managers should consider the company’s reputation among landlords and other industry professionals. Providers with positive reviews and long-standing relationships with property owners are more likely to offer reliable service and compliant equipment. Additionally, reputable companies often provide comprehensive training and support, which can be crucial for maintaining a safe and legally compliant work environment.
Ensuring Proper Operator Training and Certification
Proper operator training and certification are crucial for complying with state-specific man lift rental laws. Construction companies must ensure their operators receive comprehensive training, covering equipment operation, safety protocols, and emergency procedures. Failure to provide adequate training can result in accidents, property damage, and potential legal consequences, including debt from fines or lawsuits.
Many states require operators to undergo specific certification programs, which may include both classroom instruction and hands-on experience. These programs often cover topics such as load capacity, stability on various surfaces, and proper use of safety harnesses. Operators must demonstrate proficiency in maneuvering lifts in tight spaces, often within an inch of obstacles, to ensure safe operation in real-world scenarios.
Construction companies should maintain detailed records of operator training and certification to comply with state regulations. This documentation is essential for protecting both the company and its residents or renters in case of an incident. Regular refresher courses and updated certifications help ensure operators stay current with evolving safety standards and equipment improvements, reducing the risk of accidents and non-compliance.
Implementing Safety Protocols on the Job Site
Implementing safety protocols on job sites is crucial for compliance with state-specific man lift rental laws. Construction companies must establish clear guidelines for equipment usage, including proper setup of portable toilets and adherence to nursing regulations for on-site medical care. These protocols should be communicated in multiple languages to ensure all workers understand and follow safety procedures.
Regular safety inspections are essential to maintain compliance with state regulations. Site managers should conduct daily checks of man lifts and surrounding areas, ensuring that equipment is operated within safe distances from power lines and unstable surfaces. In states like New Jersey, specific requirements for safety zone markings and warning signs must be strictly followed to prevent accidents and regulatory violations.
Training programs should emphasize the importance of proper personal protective equipment (PPE) usage when operating man lifts. Workers must be instructed on the correct use of harnesses, hard hats, and non-slip footwear. Additionally, protocols should address emergency procedures, including how to safely lower the lift in case of power failure or operator incapacitation, ensuring preparedness for various scenarios on the job site.