Table Of Contents:
- Key Takeaways
- The Importance of Man Lift Inspections for Safety Compliance
- Pre-Rental Man Lift Inspection Checklist
- Daily Man Lift Inspection Checklist for Operators
- Identifying Common Issues During Inspections
- Strategies for Maintaining Safety Compliance
- Choosing a Reliable Man Lift Rental Company
Are you confident in your man lift inspection practices for safety compliance? This comprehensive guide will equip you with essential knowledge to ensure occupational safety and health in your construction operations. We’ll cover crucial inspection checklists, common issues to watch for, and strategies for maintaining regulatory compliance. By following our expert advice, you’ll learn how to properly inspect components like loaders and switches, and understand the importance of proper lubrication. This guide will help you choose a reliable man lift rental company and keep your worksite safe and compliant.
Key Takeaways
- Regular man lift inspections are crucial for safety compliance and preventing accidents
- Daily checks of fluid levels, hydraulic components, and safety features ensure optimal performance
- Professional inspections and operator training are essential for maintaining safety standards
- Detailed record-keeping and preventative maintenance plans help optimize equipment reliability and longevity
- Selecting a reliable rental company involves verifying compliance, assessing equipment quality, and evaluating support services
The Importance of Man Lift Inspections for Safety Compliance
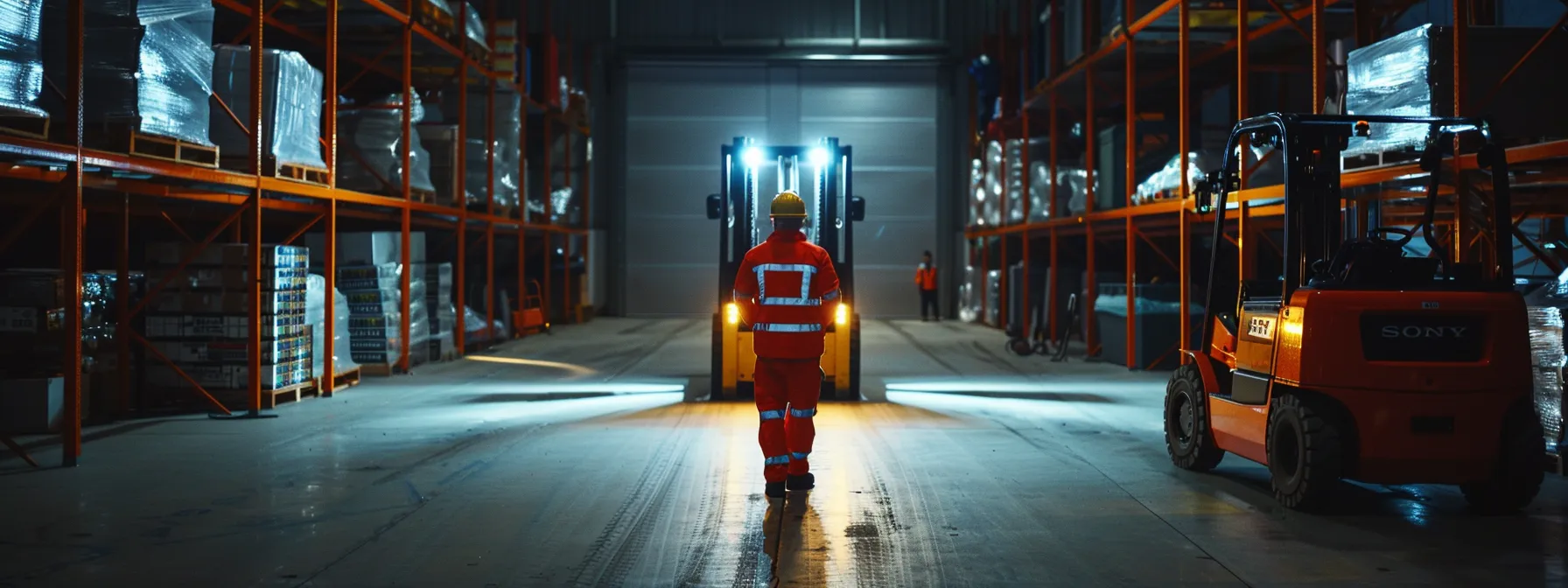
Regular man lift inspections are crucial for safety compliance, addressing legal obligations and industry standards. Neglecting inspections poses risks to workers and equipment, including potential issues with lighting, wheels, and forklift operations. Adhering to inspection protocols ensures safety, prevents accidents, and maintains proper pallet racking. These measures mitigate risks and promote a secure work environment.
Legal Obligations and Industry Standards
Legal obligations for man lift inspections stem from regulations set by the Occupational Safety and Health Administration (OSHA) and industry standards established by the American National Standards Institute (ANSI). These guidelines mandate regular maintenance checks, including tire inspections and electrical system evaluations, to ensure safe operation and prevent accidents.
Employers must adhere to specific inspection schedules outlined in ANSI standards, which often require daily, monthly, and annual inspections. These comprehensive checks cover various components, from structural integrity to hydraulic systems, and must be documented in detailed reports, often available in PDF format for easy access and record-keeping.
Compliance with these standards not only ensures worker safety but also protects companies from potential legal liabilities. Regular inspections, following ANSI guidelines, help identify and address issues before they lead to equipment failure or workplace accidents, ultimately contributing to a safer and more efficient work environment.
Risks of Neglecting Regular Inspections
Neglecting regular inspections of man lifts in equipment rental operations can lead to catastrophic equipment failures. Critical components like wire ropes and battery chargers may deteriorate unnoticed, potentially causing accidents during operation. This oversight not only endangers workers but also exposes rental companies to significant liability risks.
Inadequate maintenance checks can result in decreased equipment longevity and increased downtime. JLG Industries, a leading manufacturer of access equipment, emphasizes the importance of routine inspections to prevent unexpected breakdowns. Regular assessments of wire components and electrical systems ensure optimal performance and reduce costly repairs.
Safety compliance issues arising from neglected inspections can lead to regulatory fines and penalties. OSHA regulations mandate regular maintenance checks, including thorough examinations of wire ropes and battery systems. Failure to comply with these standards can result in severe financial consequences and damage to a company’s reputation in the equipment rental industry.
Benefits of Adhering to Inspection Protocols
Adhering to inspection protocols for man lifts ensures compliance with safety regulations and industry standards. Regular inspections by qualified inspectors help identify potential issues with aerial equipment before they become critical, reducing the risk of accidents and emergency situations. This proactive approach enhances workplace safety and protects both operators and bystanders.
Consistent inspection practices contribute to the longevity and reliability of man lift vehicles. By addressing minor issues promptly, companies can prevent costly breakdowns and extend the operational life of their equipment. This systematic approach to maintenance optimizes the performance of aerial platforms and minimizes unexpected downtime, resulting in improved efficiency and cost-effectiveness.
Proper inspection protocols foster a culture of safety within organizations. When employees observe the commitment to regular inspections, they develop a heightened awareness of safety practices. This cultivates a more responsible and safety-conscious workforce, reducing the likelihood of operator errors and promoting overall workplace safety. The benefits of adhering to inspection protocols extend beyond equipment maintenance to encompass the entire work environment:
Benefit | Impact |
---|---|
Regulatory Compliance | Avoids fines and legal issues |
Equipment Longevity | Reduces replacement costs |
Accident Prevention | Minimizes workplace injuries |
Operational Efficiency | Decreases unexpected downtime |
Pre-Rental Man Lift Inspection Checklist
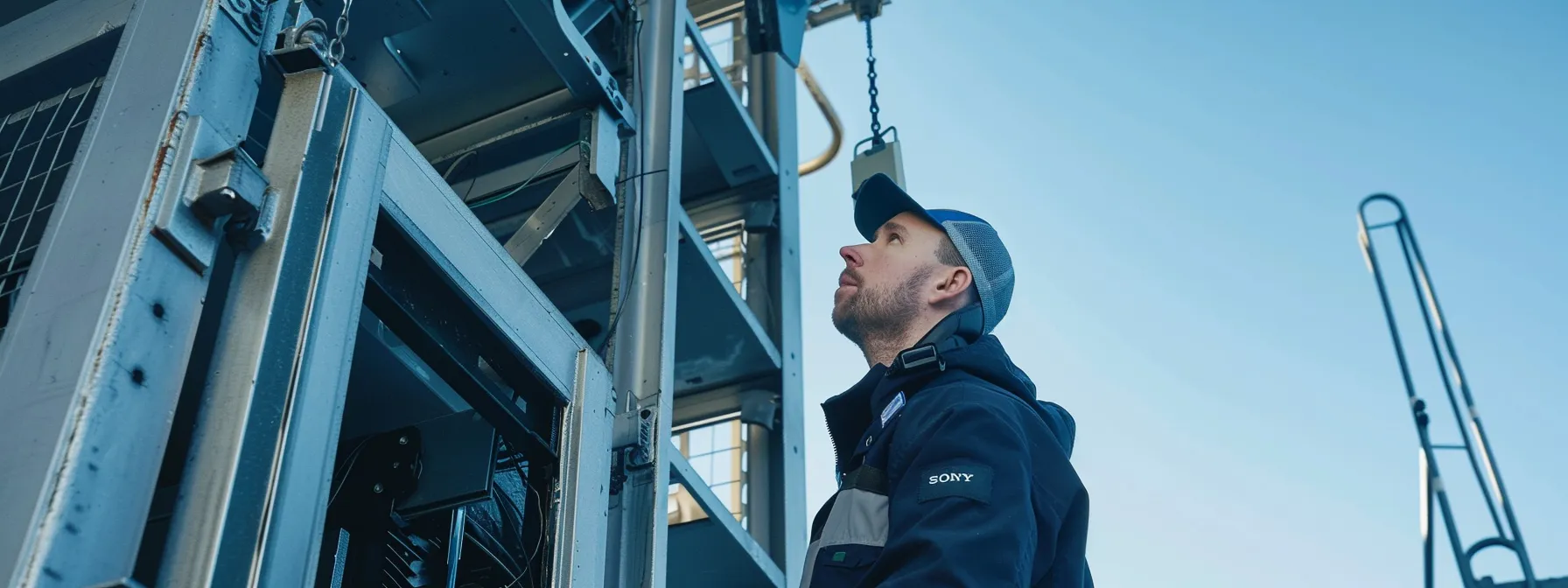
A comprehensive pre-rental man lift inspection checklist is essential for ensuring aerial lift safety and productivity. This checklist covers crucial aspects: assessing operational controls, inspecting safety features and emergency systems, evaluating structural integrity, and verifying documentation. These steps are vital for maintaining equipment health and complying with elevator safety standards.
Assess Operational Controls Thoroughly
A thorough assessment of operational controls is crucial for ensuring the safety and functionality of aerial work platforms. Inspectors must meticulously examine all control mechanisms, including the brake system, to verify their responsiveness and reliability. This comprehensive evaluation aligns with Occupational Safety and Health Administration regulations and forms a critical part of the inspection checklist.
Inspectors should test each control function individually, ensuring smooth operation and proper response times. They must pay particular attention to emergency stop buttons, level sensors, and overload warning systems. These checks help prevent accidents and equipment failures during operation, safeguarding workers and maintaining compliance with safety standards.
Documentation of the control assessment is essential for regulatory compliance and equipment maintenance records. Inspectors should record the condition and performance of each control mechanism, noting any irregularities or necessary adjustments. This detailed documentation serves as a valuable reference for future inspections and demonstrates adherence to safety protocols.
Inspect Safety Features and Emergency Systems
Thorough inspection of safety features and emergency systems is crucial for man lift rentals. Inspectors must check the condition of hydraulic fluid levels and quality, ensuring proper lubrication of bearings and gears. They should also verify the functionality of emergency lowering systems and assess the integrity of safety harness attachment points.
Evaluating the man lift‘s load capacity is essential for safe operation. Inspectors must confirm that the weight limit indicator is clearly visible and accurate. They should also examine the outriggers and stabilizers, ensuring they deploy correctly and provide adequate support during operation.
Documentation plays a vital role in safety compliance. Inspectors must verify that the man lift‘s serial number matches the documentation and that all required safety decals are present and legible. A comprehensive inspection checklist should include:
- Hydraulic system integrity check
- Emergency controls functionality test
- Load capacity verification
- Outrigger and stabilizer inspection
- Safety harness attachment point assessment
- Serial number and documentation verification
Evaluate Structural Integrity of the Equipment
Evaluating the structural integrity of aerial lifts is crucial for ensuring safe operations and effective cargo management. Inspectors must thoroughly examine the lift‘s frame, boom, and platform for signs of damage, corrosion, or wear. This assessment helps identify potential weaknesses that could compromise the equipment‘s stability during use.
A comprehensive inspection policy should include checking welds, bolts, and pivot points for any indications of stress or fatigue. Inspectors need to pay close attention to areas subject to high loads or frequent movement, as these are more prone to developing structural issues. Proper evaluation of these components is essential for maintaining the lift‘s reliability and safety standards.
Management teams should ensure that inspectors document all findings related to the lift‘s structural condition. This documentation serves as a valuable record for tracking the equipment‘s history and guiding future maintenance decisions. By prioritizing structural integrity evaluations, companies can significantly reduce the risk of accidents and extend the operational lifespan of their aerial lift fleet.
Verify Documentation and Certification Validity
Verifying documentation and certification validity is crucial for ensuring the safe operation of man lifts and scissor lifts. Inspectors must confirm that all necessary certifications, including operator licenses and equipment maintenance records, are up-to-date and properly filed. This process helps prevent potential legal issues and ensures compliance with safety regulations in material handling operations.
A thorough inspection of wear indicators on critical components is essential for maintaining scissor lift safety. Inspectors should check that all required safety decals and load capacity charts are clearly visible and legible. These visual indicators provide vital information to operators, helping them use the equipment properly and avoid overloading or misuse.
Documentation verification extends to the equipment‘s maintenance history and inspection records. Inspectors must ensure that all scheduled maintenance has been performed and documented correctly. This comprehensive review helps identify any potential issues with the scissor lift‘s components, allowing for proactive repairs and reducing the risk of equipment failure during operation.
Daily Man Lift Inspection Checklist for Operators
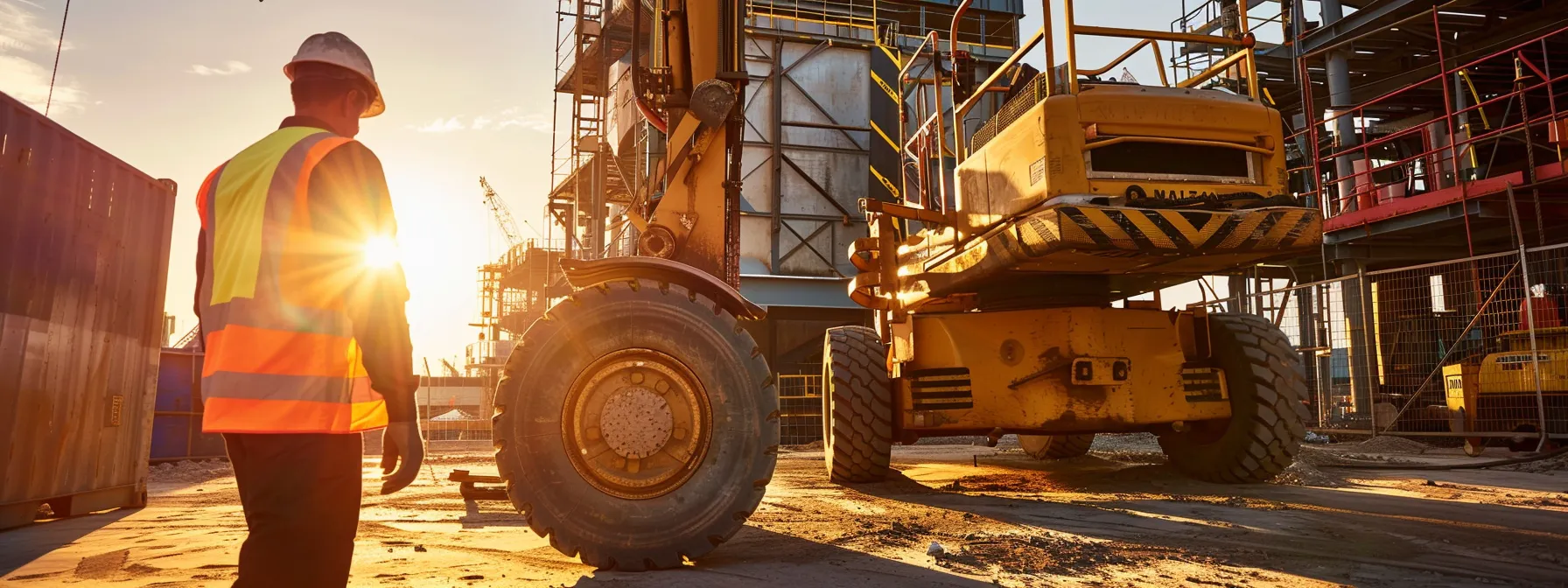
Daily man lift inspections are crucial for construction safety. Operators must check fluid levels, hydraulic components, tires, and ground support. Testing alarms and emergency stop functions ensures machine reliability. Inspecting platforms and guardrails verifies the lift‘s structural integrity. These checks maintain optimal performance and prevent accidents on job sites.
Check Fluid Levels and Hydraulic Components
Daily inspections of fluid levels and hydraulic components are crucial for maintaining the safety and performance of man lifts. Operators should check engine oil, hydraulic fluid, and fuel levels as part of their daily checklist, ensuring the lift operates efficiently throughout the workday. Proper fluid maintenance not only enhances the lift‘s performance but also extends its lifespan, potentially reducing insurance costs associated with equipment breakdowns.
Hydraulic system integrity is paramount for safe lift operation. Operators must inspect hydraulic hoses, fittings, and cylinders for signs of wear, leaks, or damage. Any issues identified during this check should be immediately reported and addressed before operating the lift. This proactive approach helps prevent accidents and ensures the tool remains in optimal working condition.
Documentation of fluid level checks and hydraulic component inspections is essential for compliance and maintenance tracking. Operators should record their findings on a standardized checklist, noting any abnormalities or maintenance performed. This documentation serves as a valuable reference for maintenance teams and can be crucial for insurance claims or safety audits related to lift operations.
Inspect Tires, Wheels, and Ground Support
Operators must thoroughly inspect tires and wheels during daily man lift checks. They should examine tire pressure, tread depth, and overall condition, noting any cuts, bulges, or excessive wear on the inspection form. Proper tire maintenance ensures optimal speed and stability during operation.
Ground support components, including outriggers and stabilizers, require careful assessment. Operators should verify that these elements deploy correctly and provide adequate support on various surfaces. Innovative Reach emphasizes the importance of this step to prevent accidents caused by uneven weight distribution.
Engine and oil checks form a crucial part of the daily inspection routine. Operators must ensure proper oil levels and look for signs of leaks or contamination. This proactive approach helps maintain the man lift‘s performance and extends its operational life, aligning with Innovative Reach’s commitment to equipment reliability.
Test Alarms and Emergency Stop Functions
Daily testing of alarms and emergency stop functions is crucial for ensuring man lift safety. Operators must verify that all warning systems, including motion alarms and tilt sensors, are functioning correctly. This step is essential for alerting workers to potential hazards and preventing accidents on job sites.
Emergency stop mechanisms require thorough inspection to guarantee immediate response in critical situations. Operators should test these functions from both the platform and ground control panels, ensuring they halt all lift movements instantly. Proper functionality of these systems is vital for operator safety and compliance with industry regulations.
Documentation of alarm and emergency stop tests is essential for maintaining safety records. Operators should note the results of these checks on their daily inspection forms, including any issues encountered or maintenance required. This information helps track the lift‘s condition over time and can be crucial for identifying potential safety concerns, even when the equipment is relocated to different Google Maps locations.
Ensure Platforms and Guardrails Are Secure
Daily inspections of platforms and guardrails are crucial for ensuring the safety of man lift operations. Operators must thoroughly check the platform floor for any damage, debris, or slippery substances that could compromise worker safety. They should also verify that all guardrails are securely fastened and free from any signs of damage or corrosion.
The integrity of platform attachments and entry gates requires careful examination. Operators should test the functionality of self-closing gates and ensure they latch properly. Any loose bolts, missing pins, or damaged welds on the platform structure must be identified and reported immediately to prevent potential accidents during lift operation.
Proper documentation of platform and guardrail inspections is essential for maintaining safety records and complying with regulations. Operators should record their findings on a standardized checklist, noting any issues or necessary repairs. This documentation serves as a critical reference for maintenance teams and demonstrates due diligence in equipment safety management:
Inspection Point | Action | Status |
---|---|---|
Platform Floor | Check for damage and cleanliness | Pass/Fail |
Guardrails | Verify secure attachment and condition | Pass/Fail |
Entry Gates | Test functionality and latching | Pass/Fail |
Attachment Points | Inspect for loose bolts or damage | Pass/Fail |
Identifying Common Issues During Inspections

Identifying common issues during man lift inspections is crucial for safety compliance and equipment reliability. This section covers detecting hydraulic leaks, recognizing electrical system malfunctions, spotting mechanical wear, and addressing safety device issues promptly. Early identification of these problems ensures optimal performance and prevents accidents on job sites.
Detect Hydraulic Leaks and Failures Early
Early detection of hydraulic leaks and failures is crucial for maintaining man lift safety and performance. Inspectors should carefully examine hydraulic hoses, fittings, and cylinders for signs of wear, damage, or fluid seepage. Regular checks help prevent unexpected equipment failures and ensure optimal lift operation on construction sites.
Innovative Reach recommends using advanced diagnostic tools to identify potential hydraulic issues before they escalate. These tools can detect minor pressure changes or fluid contamination that might not be visible during routine visual inspections. Implementing such technology enhances the accuracy of inspections and reduces the risk of equipment downtime.
Proper documentation of hydraulic system checks is essential for tracking equipment health over time. Inspectors should record detailed observations, including fluid levels, operating pressures, and any anomalies detected. This comprehensive approach to hydraulic system maintenance aligns with OSHA guidelines and helps construction companies maintain a safe and efficient fleet of man lifts:
- Inspect hydraulic hoses for cracks or abrasions
- Check fittings and connections for tightness
- Monitor fluid levels and quality
- Test hydraulic pressure and flow rates
- Examine cylinders for leaks or damage
Recognize Electrical System Malfunctions
Recognizing electrical system malfunctions in man lifts is crucial for preventing accidents and equipment failures. Inspectors should check for frayed wires, loose connections, and corrosion on battery terminals. These issues can lead to unreliable lift operation and pose significant safety risks to operators and workers on construction sites.
Innovative Reach recommends testing all electrical components, including control panels, limit switches, and warning systems, during routine inspections. Malfunctions in these areas can result in unexpected movements or failure of critical safety features. Proper documentation of electrical system checks helps track recurring issues and guides preventive maintenance schedules.
Operators should be trained to identify signs of electrical problems, such as intermittent control responses or flickering displays. Early detection of these symptoms allows for timely repairs, minimizing downtime and maintaining optimal lift performance. Regular electrical system inspections also ensure compliance with OSHA regulations and industry safety standards.
Spot Mechanical Wear and Potential Failures
Spotting mechanical wear and potential failures in man lifts requires a keen eye for detail. Inspectors should focus on critical components such as gears, chains, and bearings, looking for signs of excessive wear, misalignment, or unusual noises during operation. These indicators often precede more serious mechanical failures that could compromise the lift‘s safety and performance.
Innovative Reach emphasizes the importance of checking structural elements for cracks, deformations, or corrosion. Inspectors should pay close attention to welds, pivot points, and load-bearing components, as these areas are prone to stress-induced damage. Early detection of structural issues can prevent catastrophic failures and extend the equipment‘s operational lifespan.
Regular inspection of the lift‘s extension and retraction mechanisms is crucial for identifying potential failures. Operators should test these functions under various load conditions, noting any unusual resistance or jerky movements. Documenting these observations helps maintenance teams address issues promptly, ensuring the man lift remains reliable and safe for use on construction sites.
Address Safety Device Malfunctions Promptly
Addressing safety device malfunctions promptly is crucial for maintaining the integrity of man lift operations. Operators must immediately report any issues with limit switches, tilt sensors, or load management systems. Innovative Reach emphasizes the importance of swift action to prevent accidents and ensure compliance with OSHA regulations.
Regular testing of emergency stop buttons and descent systems is essential for identifying potential malfunctions. Inspectors should verify that these critical safety features respond instantly when activated. Any delay or failure in these systems requires immediate attention and repair before the lift can be returned to service.
Documentation plays a vital role in tracking and addressing safety device issues. Operators and inspectors should maintain detailed records of all malfunctions, repairs, and replacements. This information helps identify recurring problems and guides preventive maintenance strategies, enhancing overall equipment reliability and safety:
- Check limit switches for proper activation
- Test tilt sensors under various conditions
- Verify load management system accuracy
- Inspect emergency stop buttons for responsiveness
- Evaluate emergency descent system functionality
Strategies for Maintaining Safety Compliance
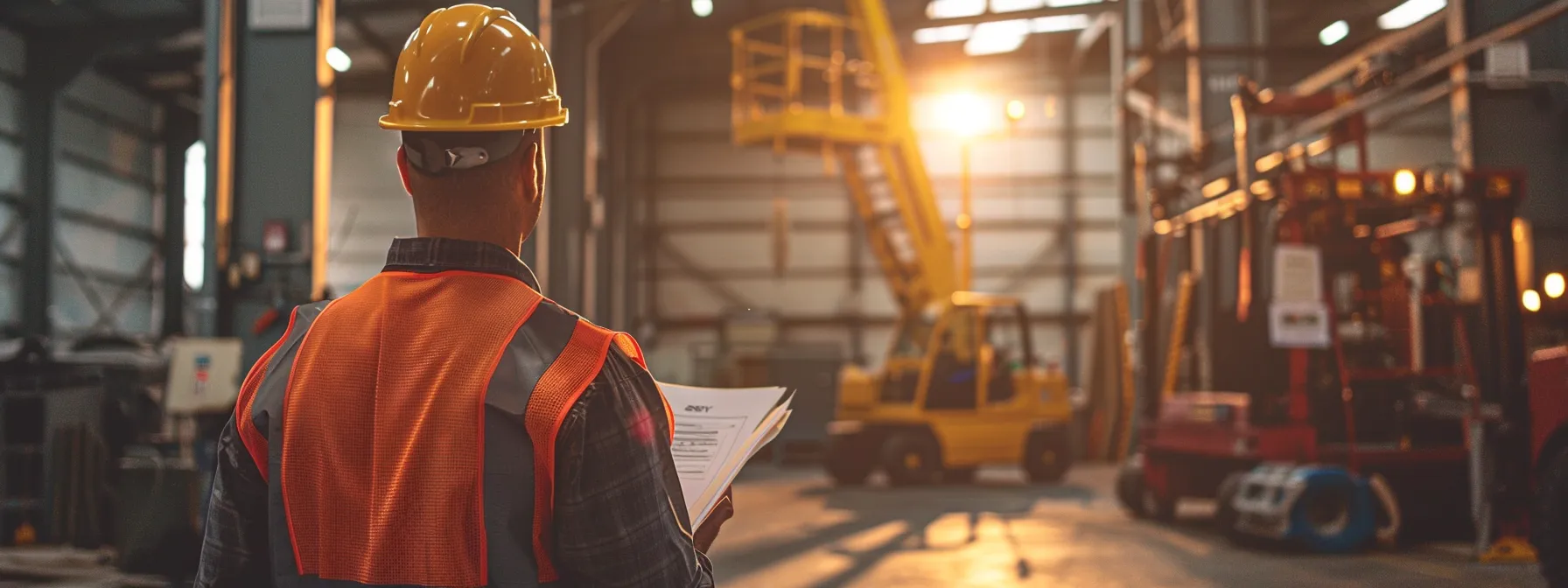
Maintaining safety compliance for man lift rentals requires a multifaceted approach. This section outlines key strategies: scheduling regular professional inspections, training operators on inspection procedures, maintaining detailed records, and implementing preventative maintenance plans. These practices ensure equipment reliability, operator competence, and adherence to safety standards, ultimately safeguarding workers and optimizing lift performance.
Schedule Regular Professional Inspections
Regular professional inspections are essential for maintaining safety compliance in man lift rentals. Innovative Reach recommends scheduling these inspections at intervals specified by manufacturers and regulatory bodies. These thorough examinations, conducted by certified professionals, ensure that all components meet safety standards and operate efficiently.
Professional inspectors utilize specialized equipment and follow comprehensive checklists to assess man lifts thoroughly. They examine critical areas such as hydraulic systems, electrical components, and structural integrity, which may not be easily evaluated during daily operator checks. This level of scrutiny helps identify potential issues before they escalate into major problems or safety hazards.
Scheduling professional inspections also provides documentation necessary for regulatory compliance and insurance purposes. These detailed reports offer a clear history of the equipment‘s condition and maintenance, demonstrating due diligence in safety practices. Companies renting man lifts should view these inspections as investments in workplace safety and equipment longevity rather than mere regulatory obligations.
Train Operators on Inspection Procedures
Effective operator training on inspection procedures is crucial for maintaining safety compliance in man lift operations. Innovative Reach emphasizes the importance of comprehensive training programs that cover daily inspection routines, equipment-specific checks, and proper documentation techniques. These programs ensure operators can identify potential issues early, reducing the risk of accidents and equipment failures.
Training should include hands-on practice with inspection checklists and equipment familiarization. Operators must learn to recognize signs of wear, damage, or malfunction in critical components such as hydraulic systems, electrical controls, and structural elements. This practical experience enhances their ability to perform thorough inspections efficiently and accurately.
Regular refresher courses and updates on new safety standards or equipment modifications are essential for maintaining operator competence. Companies should implement a system for tracking training completion and scheduling periodic reassessments to ensure all operators remain current with inspection procedures and safety protocols. This ongoing education approach helps foster a culture of safety and accountability among man lift operators.
Maintain Detailed Inspection and Maintenance Records
Maintaining detailed inspection and maintenance records is crucial for ensuring safety compliance in man lift rental operations. Companies should implement a robust record-keeping system that tracks daily inspections, routine maintenance, and any repairs performed on each piece of equipment. These records serve as a valuable resource for identifying patterns of wear or recurring issues, enabling proactive maintenance strategies.
Digital record-keeping systems offer significant advantages for managing inspection and maintenance data. Cloud-based platforms allow for real-time updates and easy access to equipment histories, facilitating efficient scheduling of maintenance tasks and inspections. This technology also enables companies to generate comprehensive reports quickly, demonstrating compliance with safety regulations during audits or inspections.
Regular analysis of inspection and maintenance records can reveal opportunities for improving equipment reliability and safety. By reviewing these records, companies can identify trends in component failures or maintenance needs, informing decisions about equipment upgrades or replacements. This data-driven approach to equipment management helps optimize the performance and longevity of man lift rentals while ensuring consistent safety standards.
Implement a Preventative Maintenance Plan
Implementing a preventative maintenance plan is crucial for ensuring the safety and reliability of man lift rentals. Innovative Reach recommends developing a comprehensive schedule that outlines regular maintenance tasks, including lubrication, component replacements, and system calibrations. This proactive approach helps identify potential issues before they escalate into major problems, reducing downtime and improving overall equipment performance.
A well-structured preventative maintenance plan should incorporate manufacturer guidelines and industry best practices. Companies should tailor their maintenance schedules to account for specific usage patterns, environmental conditions, and equipment age. Regular inspections, coupled with timely maintenance actions, can significantly extend the lifespan of man lifts and enhance their safety features.
Effective preventative maintenance relies on consistent execution and documentation. Companies should train maintenance personnel on proper procedures and ensure they have access to necessary tools and replacement parts. Implementing a digital maintenance management system can streamline the process, enabling better tracking of maintenance activities and generating alerts for upcoming service needs. A comprehensive preventative maintenance plan typically includes:
- Scheduled component replacements based on manufacturer recommendations
- Regular lubrication of moving parts to reduce wear
- Periodic calibration of safety systems and controls
- Routine inspections of structural elements and hydraulic systems
- Systematic review and updating of maintenance procedures
Choosing a Reliable Man Lift Rental Company

Selecting a reliable man lift rental company is crucial for ensuring safety and efficiency. This section explores key factors: verifying compliance with safety standards, assessing equipment quality and maintenance practices, reviewing customer feedback, and evaluating support services. These considerations help construction professionals make informed decisions when choosing a rental provider.
Confirm Compliance With Safety Standards
Confirming compliance with safety standards is crucial when selecting a man lift rental company. Reputable providers should demonstrate adherence to OSHA regulations and ANSI standards for aerial work platforms. Construction professionals should verify that rental companies maintain up-to-date certifications and conduct regular safety audits of their equipment fleet.
Rental companies should provide documentation of their compliance efforts, including records of equipment inspections, maintenance logs, and operator training programs. These documents serve as evidence of the company’s commitment to safety and can be critical in ensuring jobsite compliance. Construction managers should request and review these records before entering into a rental agreement.
Safety compliance extends beyond equipment to include operator training and support. Reliable rental companies often offer comprehensive training programs for operators, ensuring they are well-versed in the safe operation of specific man lift models. This proactive approach to safety education can significantly reduce the risk of accidents and improve overall jobsite safety.
Evaluate Equipment Quality and Maintenance Practices
Evaluating equipment quality and maintenance practices is crucial when selecting a man lift rental company. Construction professionals should inspect the condition of the rental fleet, focusing on factors such as age, wear, and overall appearance. Well-maintained equipment typically exhibits clean, properly functioning components and up-to-date safety features.
Rental companies with robust maintenance practices often provide detailed service records for their equipment. These records should demonstrate regular inspections, timely repairs, and adherence to manufacturer-recommended maintenance schedules. Construction managers can request this documentation to assess the reliability and safety of the man lifts they plan to rent.
On-site visits to the rental company’s facilities can offer valuable insights into their maintenance practices. During these visits, construction professionals can observe the cleanliness of the maintenance area, the organization of spare parts, and the professionalism of the maintenance staff. Companies that invest in high-quality equipment and maintain it meticulously are more likely to provide reliable and safe man lifts for rental.
Consider Customer Reviews and Testimonials
Customer reviews and testimonials provide valuable insights into a man lift rental company’s reliability and service quality. Construction professionals should carefully examine feedback from previous clients, focusing on comments about equipment condition, safety practices, and customer support. These firsthand accounts can reveal potential issues or highlight exceptional service that may not be apparent from company marketing materials.
Online platforms and industry forums often feature detailed reviews of rental companies, offering a broader perspective on their performance. Construction managers should pay attention to recurring themes in customer feedback, such as punctuality of deliveries, responsiveness to maintenance requests, and the overall condition of rented equipment. This information can help in making informed decisions when selecting a rental provider.
While considering reviews, it’s important to assess their credibility and relevance. Recent testimonials from similar construction projects carry more weight than older or unrelated feedback. Construction professionals should also reach out to industry peers for recommendations, as personal referrals often provide the most reliable insights into a rental company’s performance and safety standards.
Assess Availability of Support and Service Offerings
Assessing the availability of support and service offerings is crucial when selecting a man lift rental company. Construction professionals should evaluate the rental provider’s response times for equipment breakdowns and maintenance requests. A reliable company will offer 24/7 emergency support and have a clear protocol for addressing on-site issues promptly.
The range of services offered by the rental company can significantly impact project efficiency. Look for providers that offer comprehensive packages, including delivery, setup, and operator training. These value-added services can streamline operations and enhance safety on construction sites. Additionally, companies that provide regular maintenance checks during the rental period demonstrate a commitment to equipment reliability and customer satisfaction.
Technical support capabilities are another critical factor to consider. Rental companies should have knowledgeable staff available to answer questions about equipment operation and troubleshoot issues. The availability of on-site technicians or remote diagnostic services can minimize downtime and ensure optimal performance of rented man lifts. When evaluating support offerings, construction managers should consider the following factors:
- Availability of 24/7 emergency support
- Response time for maintenance requests
- On-site technician services
- Equipment delivery and setup assistance
- Operator training programs
- Remote diagnostic capabilities